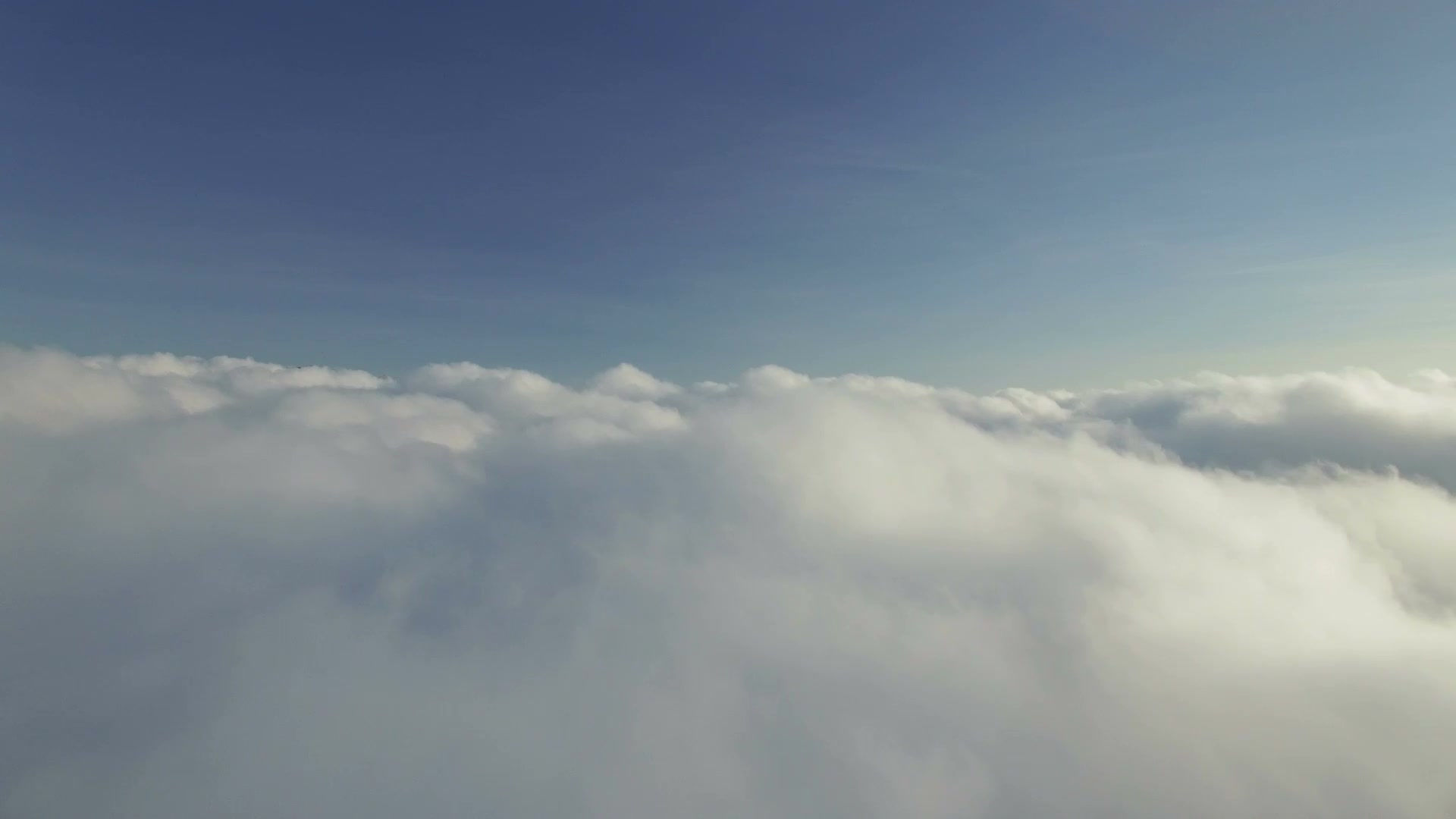
How CNC Machining Improves Watch Part Precision
Ultem CNC machining transforms raw polyetherimide stock into precision components that outperform traditional metals while weighing 70% less. This amber-colored thermoplastic maintains structural integrity at 200°C, resists aggressive chemicals, and delivers exceptional electrical insulation—but only when machined with cutting speeds between 80-500 rpm and specialized coolant systems that prevent catastrophic stress cracking failures.
Engineering teams at Yijin Hardware have refined Ultem machining protocols over thousands of production hours, developing parameter sets that consistently deliver ±1µm surface finishes for mission-critical aerospace, medical, and electronics applications. This guide distills that expertise into actionable insights that eliminate common failure modes while maximizing material performance.
Why Are Engineers Choosing Ultem Over Traditional Materials?
The shift toward Ultem represents a fundamental change in how engineers approach high-performance applications. Unlike conventional engineering plastics that compromise either thermal resistance or mechanical strength, Ultem delivers both characteristics through its unique polyetherimide molecular structure.
Performance Breakthrough Characteristics:
Ultem's molecular formula C₃₇H₂₄O₆N₂ creates a rigid backbone that maintains dimensional stability across temperature extremes. While aluminum yields strength at elevated temperatures, Ultem components retain their precision fit and finish throughout thermal cycling that would cause metal fatigue.
Weight Revolution in Design:
-
Aerospace Weight Savings: 70% lighter than equivalent aluminum components
-
Automotive Efficiency: Reduces rotating mass in engine compartments
-
Medical Portability: Enables handheld devices previously requiring desktop platforms
-
Electronics Miniaturization: Supports compact designs impossible with metal housings
Chemical Immunity Advantages: Traditional metals corrode, conventional plastics dissolve, but Ultem maintains integrity when exposed to:
-
Automotive fuels and lubricants
-
Medical sterilization chemicals
-
Industrial solvents and acids
-
Electronic cleaning compounds
Electrical Superiority: Ultem's dielectric strength exceeds 500 V/mil, maintaining insulation properties across wide frequency ranges where metals require additional insulation layers that add weight and complexity.
What Happens When Ultem Machining Goes Wrong?
Understanding failure modes reveals why Ultem demands specialized machining approaches that differ fundamentally from both metal and conventional plastic processing.
The Delayed Failure Phenomenon: Ultem's most dangerous characteristic involves stress cracking that occurs hours or days after machining completion. Parts pass initial inspection, ship to customers, then fail catastrophically when exposed to service environments. This delayed failure mechanism stems from molecular-level damage during improper machining operations.
Heat-Induced Molecular Degradation: Excessive cutting temperatures cause polymer chain scission that weakens material structure without visible surface damage. Components appear perfect but contain compromised molecular bonds that fail under service loads.
Coolant Contamination Disasters: Petroleum-based coolants penetrate Ultem's molecular structure, creating stress concentration points that propagate cracks under minimal loading. A single exposure to inappropriate coolant can render parts unusable weeks later.
Glass Fiber Machining Challenges: Glass-filled Ultem grades contain 30% glass fibers that act like microscopic sandpaper, destroying cutting tools while generating heat that degrades the polymer matrix. Standard machining parameters cause rapid tool failure and part rejection.
Surface Integrity Complications: Unlike metals that show obvious machining defects, Ultem can appear perfectly machined while containing subsurface damage that compromises long-term performance and safety margins.
How Do Material Grades Transform Machining Requirements?
Each Ultem grade presents distinct machining challenges requiring tailored approaches for successful manufacturing outcomes.
Ultem 1000: The Precision Baseline
Unfilled Ultem 1000 provides the most forgiving machining characteristics while delivering exceptional property combinations for demanding applications.
Machining Sweet Spot Parameters:
-
Milling Operations: 350-450 rpm with 0.2-0.35 mm/r feed rates
-
Turning Applications: 375 rpm optimal with 0.15-0.25 mm/r feeds
-
Drilling Protocols: 40-60 rpm with peck cycles every 0.5x diameter
-
Surface Speed: 75-85 m/min for optimal tool life balance
Tool Selection Strategies: High-speed steel tools provide adequate performance for prototype quantities, while carbide tooling becomes essential for production volumes exceeding 50 pieces. Sharp cutting edges prevent heat buildup that causes molecular degradation.
Applications Optimization: Medical device components benefit from Ultem 1000's biocompatibility and sterilization resistance. Electronics housings leverage superior dielectric properties. Food processing equipment utilizes chemical resistance and FDA compliance.
Ultem 2300: Glass-Reinforced Complexity
30% glass fiber reinforcement transforms Ultem into an engineering powerhouse while creating significant machining challenges requiring specialized techniques.
Modified Parameter Requirements:
-
Reduced Speeds: 100-150 rpm maximum to prevent glass fiber pullout
-
Increased Feeds: 0.1-0.5 mm/r to maintain chip formation integrity
-
Mandatory Cooling: Glass fiber cutting generates excessive heat
-
Tool Material: PCD or carbide essential due to abrasive glass content
Glass Fiber Behavior Management: Glass fibers create anisotropic material properties that affect machining forces and surface finish quality. Cutting direction relative to fiber orientation influences tool wear patterns and dimensional accuracy.
Enhanced Performance Applications: Structural aerospace brackets utilize the 300% stiffness increase over unfilled grades. Automotive under-hood components benefit from improved creep resistance. Industrial machinery parts leverage enhanced wear characteristics.
Ultem 9085: Aerospace Certification Standards
This specialized grade meets stringent aerospace requirements while presenting unique machining considerations for certified applications.
Certification Requirements:
-
FST (Flame, Smoke, Toxicity) compliance for aircraft interiors
-
Traceability documentation throughout manufacturing process
-
Enhanced mechanical properties for weight-critical applications
-
Low outgassing characteristics for spacecraft environments
Machining Protocol Modifications: Aerospace applications demand documented process control with parameter verification and statistical process monitoring to maintain certification compliance.
Which Cutting Tools Deliver Consistent Ultem Results?
Tool selection directly impacts surface quality, dimensional accuracy, and long-term part performance through its influence on cutting temperatures and chip formation.
Advanced Tool Material Selection
Polycrystalline Diamond (PCD) Supremacy: PCD tools provide 10-50x longer tool life compared to carbide when machining glass-filled grades. The extremely sharp cutting edge minimizes cutting forces while the thermal conductivity removes heat from the cutting zone.
Carbide Tool Optimization: Submicron grain carbide with specialized coatings offers cost-effective performance for production applications. TiAlN coatings provide thermal stability while maintaining sharp cutting edges.
High-Speed Steel Applications: HSS tools remain viable for prototype and low-volume production of unfilled grades, offering flexibility for complex geometries and interrupted cuts.
Cutting Edge Geometry Secrets
Rake Angle Engineering: Positive rake angles reduce cutting forces and heat generation but must be balanced against edge strength requirements. 15-20° positive rake optimal for unfilled grades, reduced to 10-15° for glass-filled variants.
Relief Angle Optimization: Relief angles prevent rubbing and heat buildup while maintaining edge strength. 12° relief angles for unfilled grades, reduced to 8° for glass-filled materials to prevent edge chipping.
Edge Radius Control: Sharp edges (0.005-0.010" radius) essential for clean cutting without material smearing. Larger edge radii cause material burnishing and heat generation that degrades surface integrity.
Chip Breaker Design: Appropriate chip breaking prevents long, stringy chips that can wrap around rotating components and cause surface damage during part removal.
What Coolant Systems Prevent Catastrophic Failures?
Coolant selection represents the most critical factor separating successful Ultem machining from expensive failures that manifest weeks after production completion.
Approved Coolant Chemistry
Water-Soluble Synthetic Coolants: Non-aromatic synthetic coolants provide optimal thermal management without chemical attack on polymer structure. These formulations offer excellent lubricity while maintaining chemical neutrality.
Mineral Oil Prohibition: Petroleum-based coolants cause environmental stress cracking through molecular penetration. Even trace contamination from previous metal cutting operations can cause delayed failures.
Chlorinated Compound Dangers: Any chlorinated solvents cause immediate stress cracking initiation. Cleaning solvents, degreasers, and cutting fluids containing chlorine must be completely eliminated from Ultem manufacturing areas.
Application Methodology
Flood Coolant Systems: High-volume coolant application provides maximum heat removal while flushing chips from cutting zones. Filtration systems maintain coolant purity and prevent contamination buildup.
Mist Cooling Applications: Air-coolant mist systems provide targeted cooling with minimal liquid application, reducing contamination risks while maintaining thermal control for precision operations.
Compressed Air Alternatives: Clean, dry compressed air removes heat and chips without liquid contamination concerns. Particularly effective for drilling operations and finish machining.
Through-Tool Coolant Benefits: Coolant delivery directly to cutting edges maximizes heat removal efficiency while improving chip evacuation from deep holes and complex geometries.
How Do Processing Conditions Affect Long-Term Performance?
Environmental factors during machining significantly impact final part properties and service life performance.
Thermal Management Strategies
Cutting Zone Temperature Control: Maintaining cutting temperatures below 150°C prevents molecular degradation while preserving material properties. Infrared monitoring systems provide real-time temperature feedback for parameter adjustment.
Workpiece Temperature Stability: Thermal expansion during machining can cause dimensional errors requiring compensation in fixture design and machining sequences.
Ambient Environment Control: Climate-controlled machining environments ensure consistent material properties while preventing moisture absorption that affects dimensional stability.
Stress State Management
Residual Stress Minimization: Proper machining sequences minimize clamping stresses while maintaining workpiece rigidity. Stress concentration areas require special attention to prevent crack initiation.
Annealing Process Integration: Post-machining stress relief through controlled annealing removes residual stresses while restoring optimal material properties. Temperature profiles must be precisely controlled to prevent property degradation.
Fixturing Considerations: Workholding systems must support parts without inducing stresses that cause distortion or cracking. Soft jaws and distributed clamping forces prevent stress concentration.
Where Does Ultem Excel in Critical Applications?
Understanding application-specific requirements enables optimal material grade selection and machining parameter development for maximum performance outcomes.
Aerospace Mission-Critical Components
Aircraft Interior Safety Systems: Ultem components in aircraft interiors must meet FST requirements while maintaining structural integrity throughout service life. Machined components include seat mechanisms, tray tables, and electrical housings that directly impact passenger safety.
Engine Compartment Applications: Under-hood aerospace components utilize Ultem's thermal stability and chemical resistance for fuel system components, electrical connectors, and structural brackets exposed to extreme operating conditions.
Weight-Critical Structures: Machined Ultem brackets and mounts provide 70% weight savings compared to aluminum equivalents while maintaining comparable strength characteristics essential for aircraft performance and fuel efficiency.
Medical Device Precision Manufacturing
Surgical Instrument Components: Reusable surgical instruments require materials that withstand repeated sterilization cycles without degradation. Machined Ultem components maintain dimensional accuracy and surface finish through hundreds of autoclave cycles.
Diagnostic Equipment Housings: Precision medical electronics require electromagnetic shielding and chemical resistance that Ultem provides while enabling complex internal geometries impossible with metal housings.
Implantable Device Components: Biocompatible Ultem grades enable machined components for implantable devices requiring long-term biocompatibility and dimensional stability within the human body.
Electronics Thermal Management
High-Frequency Applications: Ultem's stable dielectric properties across wide frequency ranges enable precision-machined components for telecommunications and radar systems where electrical performance directly impacts system functionality.
Heat Exchanger Components: Machined Ultem heat exchangers provide corrosion resistance and thermal stability for electronic cooling systems while enabling complex internal geometries that optimize heat transfer efficiency.
Power Electronics Isolation: High-voltage applications require electrical isolation that machined Ultem components provide while maintaining mechanical strength and thermal stability under extreme operating conditions.
What Advanced Techniques Optimize Surface Quality?
Surface finish quality directly impacts part performance, particularly in applications requiring sealing, electrical contact, or optical clarity.
Precision Finishing Strategies
Multi-Pass Machining Sequences: Roughing operations remove bulk material at higher feed rates, while finishing passes at reduced parameters achieve target surface finishes. This approach minimizes heat buildup while maximizing productivity.
Tool Path Optimization: Climb milling provides superior surface finishes by eliminating tool rubbing and minimizing cutting forces. Constant chip load programming maintains consistent surface quality throughout complex geometries.
Spindle Speed Harmonics: Avoiding resonant frequencies prevents chatter that causes surface irregularities and tool wear. Spindle speed selection must consider part geometry and fixturing natural frequencies.
Surface Treatment Options
Mechanical Polishing Techniques: Progressive abrasive polishing achieves mirror finishes for optical applications while maintaining dimensional accuracy. Proper technique prevents stress concentration and surface damage.
Chemical Smoothing Processes: Controlled chemical treatments can improve surface finish while maintaining dimensional tolerance. Solvent selection must avoid compounds that cause stress cracking.
Texture Application Methods: Controlled surface texturing through specialized tooling or post-processing creates specific surface characteristics for improved adhesion or reduced friction applications.
How Do Quality Systems Ensure Repeatable Results?
Comprehensive quality control systems prevent failures while ensuring consistent part performance across production quantities.
Statistical Process Control Implementation
Parameter Monitoring Systems: Real-time monitoring of cutting forces, temperatures, and vibration levels enables immediate process adjustment when parameters drift outside acceptable ranges.
Dimensional Verification Protocols: Coordinate measuring machines verify critical dimensions while surface finish measurement ensures quality standards are maintained throughout production runs.
Material Property Confirmation: Incoming material inspection verifies grade specifications and properties before machining begins, preventing costly failures from substandard materials.
Traceability Documentation
Process Record Maintenance: Complete documentation of machining parameters, tool changes, and environmental conditions enables problem diagnosis and process improvement opportunities.
Material Certification Tracking: Full traceability from raw material through finished parts supports aerospace and medical device certification requirements while enabling rapid response to quality issues.
Performance Validation Testing: Statistical sampling and testing verify that machined parts meet all specification requirements while identifying process improvements that enhance quality and efficiency.
What Emerging Technologies Shape Ultem Machining's Future?
Advanced manufacturing technologies continue expanding possibilities for Ultem component production while improving quality and efficiency outcomes.
Smart Manufacturing Integration
Adaptive Process Control: Machine learning algorithms optimize cutting parameters in real-time based on tool wear patterns, material response, and quality requirements, maintaining optimal performance throughout tool life.
Predictive Maintenance Systems: Vibration analysis and thermal monitoring predict tool failure before quality degradation occurs, eliminating scrap while maximizing tool utilization and productivity.
Automated Quality Inspection: In-process measurement systems verify dimensions during machining, enabling immediate correction before parts are completed, reducing scrap and improving efficiency.
Advanced Tooling Developments
Nanocrystalline Tool Coatings: Next-generation tool coatings provide enhanced thermal stability and wear resistance specifically optimized for polymer machining applications.
Hybrid Manufacturing Processes: Combining additive manufacturing with CNC machining enables complex internal geometries while maintaining precision external surfaces and critical dimensional features.
Cryogenic Cooling Systems: Ultra-low temperature cooling systems provide enhanced thermal control while eliminating liquid coolant contamination concerns that affect long-term part performance.
When Should You Partner with Ultem Machining Specialists?
Professional Ultem machining services provide expertise, equipment, and quality systems that ensure project success while minimizing development time and risk.
Technical Expertise Requirements
Material Science Knowledge: Deep understanding of polymer behavior, grade selection, and processing requirements ensures optimal outcomes for specific application requirements and performance criteria.
Parameter Development Capabilities: Extensive experience enables rapid parameter optimization for new applications while minimizing development costs and time-to-market delays.
Quality System Implementation: Professional services provide comprehensive documentation, testing, and certification support required for regulated industries and critical applications.
Equipment and Facility Advantages
Dedicated Polymer Processing: Specialized facilities prevent cross-contamination from metal cutting operations while maintaining environmental controls necessary for consistent results.
Advanced Process Monitoring: Investment in monitoring and control systems enables process optimization and quality assurance that exceeds capabilities of general-purpose machine shops.
Comprehensive Testing Capabilities: Material testing, dimensional verification, and performance validation ensure parts meet all specification requirements before delivery to customers.
Why Yijin Hardware Leads Ultem Manufacturing Excellence
Yijin Hardware's specialized Ultem machining capabilities combine decades of polymer processing experience with state-of-the-art equipment and comprehensive quality systems. Our dedicated polymer facility eliminates contamination risks while our technical team optimizes parameters for each specific application requirement.
From prototype development through high-volume production, we deliver precision Ultem components that exceed performance expectations while meeting the most demanding certification requirements across aerospace, medical, automotive, and electronics industries.
Transform your next project with precision Ultem machining expertise. Contact our engineering team to discover how our specialized capabilities can optimize your designs for performance, reliability, and cost-effectiveness that sets new industry standards.
Find Us:
https://medium.com/@services297/4-reasons-cnc-milling-is-popular-in-manufacturing-489120945377
https://www.skillshare.com/en/profile/Skillshare%20Member-/687363367
https://yijin-hardware-106510.weeblysite.com/
https://www.canva.com/design/DAGpYfhrpmE/EBJyPxZ3KrPYJM5LBlwyzA/edit
http://www.nim72996.nimbosite.com.au/what-makes-rapid-prototyping-vital-for-innovation.htm
https://colab.research.google.com/drive/1JHJZvCWduXdk0dupeD_tN20y2m60xXll?usp=sharing
https://sites.google.com/view/yijinsoau/home
https://yijinsoau.jimdosite.com
https://wakelet.com/wake/cIdqL2u7k_6ejk7lBcFQf
https://www.metooo.io/e/why-cnc-turning-is-important-for-custom-parts